Perfect Place For Best Quality & Innovation
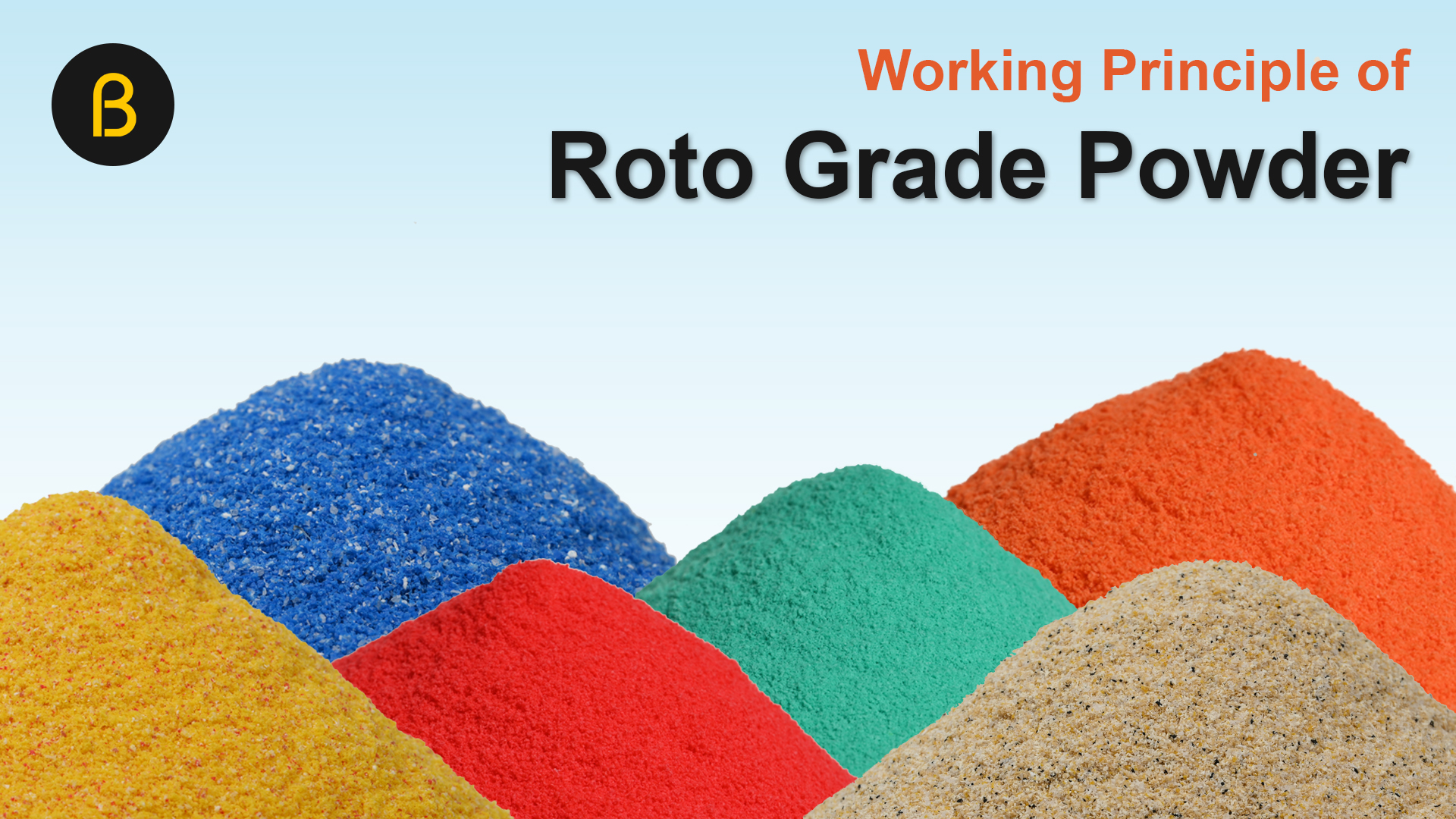
Working Principle of Roto Grade Powder
The working principle of roto grade powder in rotational moulding involves several key steps:
Powder Loading
The roto grade powder, which is a fine granular material, is loaded into a hollow mould. The mould is typically made of metal and has a specific shape and size corresponding to the desired final product.
Mould Heating
The loaded mould is heated to a controlled temperature using an oven or heating chamber. The heating process is crucial for the powder to melt and uniformly coat the inner surface of the mould.
Powder Fusion
As the mould rotates around multiple axes, the powder is subjected to centrifugal forces, which cause it to adhere to the heated mould surface. The heat melts the powder particles, and they fuse together to form a solid layer.
Wall Thickness Control
The speed of rotation and the duration of heating determine the thickness of the formed layer. The mould's design, including the presence of ribs or other features, can also influence the distribution of the molten powder and, thus, the wall thickness of the final product.
Cooling and Solidification
After the desired wall thickness is achieved, the mould is cooled using air or water. The cooling solidifies the molten powder, transforming it into a solid plastic part with the desired shape and dimensions.
Part Removal
Once the cooling process is complete, the mould is opened, and the finished part is removed. Sometimes, the part may require additional trimming or finishing operations to remove any excess material or improve the surface quality.
The working principle of roto grade powder relies on the melting and fusion of the powder particles under controlled heat and rotational motion. The centrifugal forces help distribute the molten material uniformly within the mould, ensuring consistent wall thickness throughout the part. The cooling phase solidifies the molten powder, forming a solid plastic product with the desired shape and properties.
It is important to note that the working principle may vary slightly depending on the specific rotational moulding equipment, process parameters, and the properties of the roto grade powder being used.
Troubleshooting Guide for Rotational Moulding Grade Powder
When working with rotational moulding grade powder, you may encounter various issues or challenges during the moulding process. Here’s a troubleshooting guide to help you identify and address common problems:
- Possible Causes: Insufficient heating, incorrect heating cycle, inadequate rotation speed, improper powder formulation, contaminated powder.
- Troubleshooting Steps:
- Verify that the mould is heated to the recommended temperature and the heating cycle is appropriate for the powder.
- Ensure that the rotation speed is sufficient to distribute the molten material evenly.
- Check the powder formulation for any inconsistencies or compatibility issues.
- Examine the powder for any contaminants or foreign particles and ensure proper storage conditions.
- Possible Causes: Inadequate heating or cooling, improper powder distribution, poor mould release, air entrapment, contaminated powder.
- Troubleshooting Steps:
- Review the heating and cooling cycles to ensure proper temperature control.
- Check for proper powder distribution inside the mould to avoid thin or thick spots.
- Use appropriate mould release agents to facilitate part removal.
- Ensure that the mould is properly vented to prevent air entrapment.
- Inspect the powder for any contaminants that could contribute to surface defects.
- Possible Causes: Non-uniform cooling, insufficient cooling time, uneven wall thickness, excessive mould temperature.
- Troubleshooting Steps:
- Evaluate the cooling process and adjust the cooling time to allow for uniform solidification.
- Ensure that the wall thickness is consistent throughout the part to prevent differential cooling.
- Possible Causes: Inadequate mould release, excessive mould temperature, improper cooling, excessive dwell time.
- Troubleshooting Steps:
- Apply a suitable mould release agent to facilitate part release from the mould.
- Check the mould temperature to ensure it is within the recommended range.
- Adjust the cooling process to prevent the part from sticking to the mould.
- Avoid excessive dwell time that could cause the molten material to bond with the mould surface.
- Possible Causes: Insufficient powder loading, inadequate rotation speed, improper powder distribution, mould design issues.
- Troubleshooting Steps:
- Ensure that the mould is properly loaded with the required amount of powder for the desired part size and thickness.
- Adjust the rotation speed to promote proper powder distribution and filling of the mould.
- Evaluate the mould design for any restrictions or geometrical issues that may impede powder flow.
- Possible Causes: Improper mixing of pigments or additives, uneven powder distribution, contamination.
- Troubleshooting Steps:
- Thoroughly mix pigments or additives with the powder to achieve a uniform color dispersion.
- Verify that the powder is evenly distributed within the mould to ensure consistent coloring.
- Check for any contamination sources that may affect the color of the final product.
If troubleshooting steps do not resolve the issues, it is recommended to consult with experts, such as material suppliers or rotational moulding professionals, who can provide further guidance based on their experience and knowledge of specific rotational moulding grade powders.